Aluminum alloy has been widely used in various fields due to its advantages such as low density, high specific strength, and good processability. In order to achieve the effect of energy saving and weight reduction, developed countries such as the United States, Japan and Western Europe are constantly increasing the use of aluminum alloys. The research and development efforts of forging materials and their processes, and aluminum alloy forging technology is also regarded as a core technology to focus on support and development.
Since 1956, the world's aluminum output has consistently ranked first among non-ferrous metals. The current world output of aluminum processed materials is 30 million tons per year, of which plates, strips and foils account for 57%, and extruded materials account for 38%. Due to the high cost of aluminum alloy forged materials and the difficult production technology, they are only used in particularly important stress-bearing parts, so the proportion of processed materials is small, 2.5%. With the continuous development of the automobile industry, the requirements for lightweight automobiles are getting higher and higher. According to reports, for every 10% reduction in car quality, fuel consumption can be reduced by 6% to 8%. Therefore, lightweight materials represented by aluminum alloys are increasingly used in auto parts. It is estimated that the global annual demand for aluminum forgings is as high as 1 million tons, while the current annual output in the world is only about 800,000 tons, which cannot yet meet the market demand. In the automotive industry, the current use of aluminum alloy wheels has reached billions, and it is still growing at a rate of 20% every year.
The aluminum alloy triangle arm is a key component of the automobile steering system. Its shape is complex and it is difficult to form. This article will introduce in detail an automatic aluminum alloy forging production line from the perspective of process and equipment.
Characteristics of forging process of aluminum alloy
⑴The plasticity is low.
The plasticity of aluminum alloy is greatly affected by alloy composition and forging temperature, and the sensitivity of plasticity to deformation speed varies with the content of alloy elements. When the content of alloy elements increases, the plasticity of aluminum alloy continues to decrease and is sensitive to deformation speed. The degree is also enhanced. Most aluminum alloys are positive strain rate sensitive materials, that is, the flow stress decreases as the deformation rate decreases. Therefore, for large aluminum alloy forgings for aviation, hydraulic or hydraulic presses are often used for forming, and for small and medium forgings, spirals can be used. Manufacture of presses or mechanical presses.
⑵ Strong adhesion.
Because aluminum and iron can be solid-solved, aluminum alloys often stick to molds during the forging process. It is generally believed that spindle oil can have a better lubricating effect. In recent years, American companies such as Acheson have also developed aluminum alloy lubricants suitable for industrial applications. There are also domestic companies that formulate their own oil-based or water-based lubricants, with good results.
⑶Narrow forging temperature range.
The forging temperature range of most aluminum alloys is within 150°C, and some are even only 70°C. Therefore, in the forging production, it is often necessary to use multiple heating methods to ensure that the aluminum alloy has good forgeability. In particular, aerospace and military products with strict product performance requirements are often produced by isothermal forging in the final forming.
⑷The deformation of the process is small.
Aluminum alloy forging generally does not allow small processes and large deformations to avoid coarse crystals or cracks. Therefore, it is often necessary to allocate the total deformation reasonably. The billeting process has a greater impact on the forming results of the final product. Since the temperature of the workpiece is often lower than the required forging temperature after several procedures, it needs to be heated again.
Design of forging process of aluminum alloy control arm
Recently, Beijing Institute of Mechanical and Electrical Technology developed a forging process for aluminum alloy control arms for automobiles, and established an automatic forging production line for aluminum alloy control arms based on this, which has been handed over to customers for use.
The forging process of this product is: intermediate frequency heating → roll forging → bending, flattening → secondary heating → pre-forging, final forging → trimming, punching, and correction.
Generally speaking, forging process is for metal forming and combined with CNC machining in the later stage, and then doing some precision machining in order to control tolerance and accuracy.
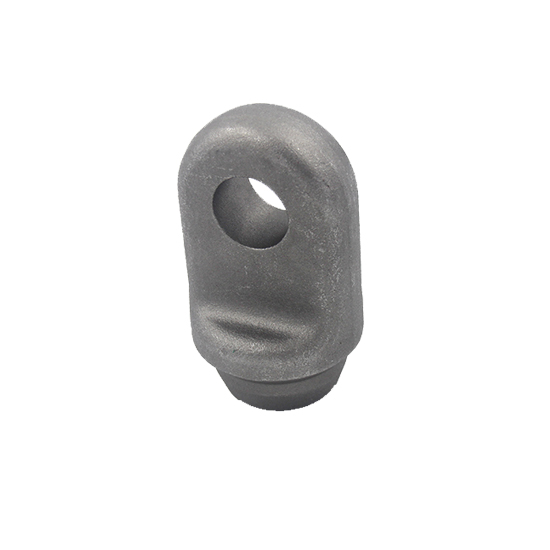
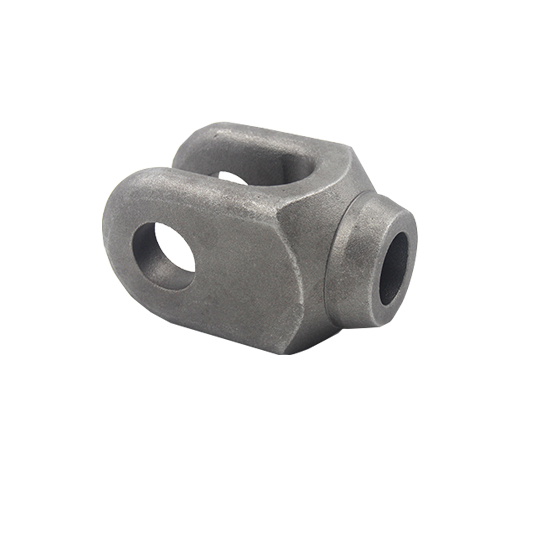
---------------------------------------------------END----------------------------------------------------------------
Edit By Rebecca Wang